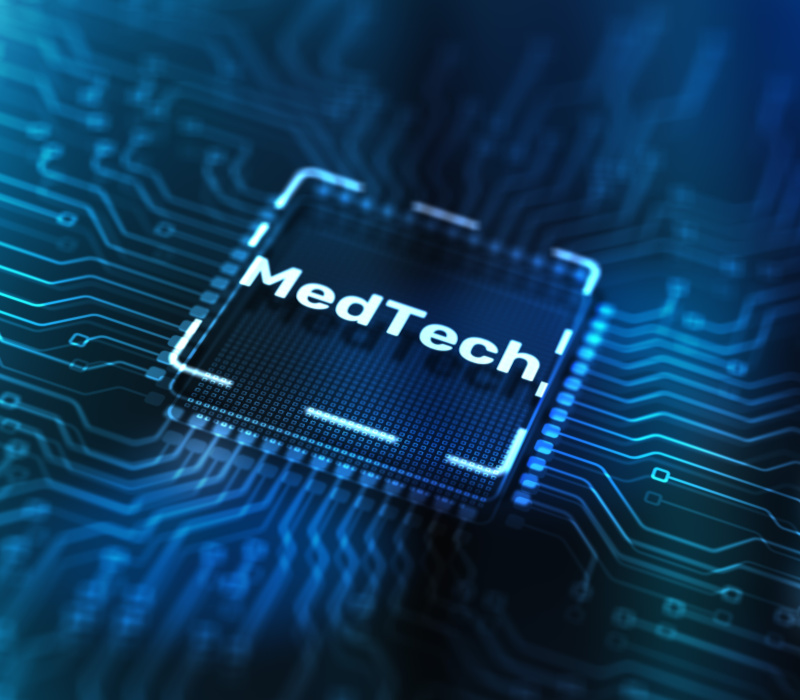
Contract manufacture of electronics for the medical industry
Any contract electronics manufacturer for the medical industry should use methods and solutions that allow them to maintain the highest possible quality standards for the components they make. After all, equipment used in medical facilities must not only work as effectively as possible, but also guarantee the safety of patients and operators. There is no room for compromise here. Therefore, electronics manufacturers are increasingly expected to have specific experience and official certificates demonstrating that they meet key standards.
Every manufacturer of medical equipment must ensure that their products meet the requirements imposed by EU regulations. Even if they outsource part of the manufacture to third-party companies, they are responsible for the quality of the finished equipment. For this reason, they seek out contract electronics manufacturers who are concerned with the superior quality and safety of manufactured components.
Medical industry – key requirements
According to the latest regulations, medical device manufacturer is required to have implemented, among other things, quality management and risk management systems enabling unique UDI identification codes to be assigned to the devices and allowing post-marketing surveillance. At the same time, they should carry out clinical assessments, conduct conformity assessment procedures and prepare technical documentation.
Some of these obligations have to be met by contract electronics manufacturers, which makes it crucial to find a supplier with the right competence and technical background.
Medical equipment – safety first
Because medical equipment is used not only in laboratories and diagnostics, but also for health monitoring and treatment, it must be as safe as possible. The risk of electrical shocks, burns and cardiac arrhythmias, etc., which can potentially affect patients in the event that equipment fails, is minimised at the manufacturing stage. At the same time, the risk of uncontrolled radiation emitted by some medical instruments is reduced, protecting operators.
Therefore, it is essential that top-quality components resistant to, for example, moisture, vibration or temperature changes be used as required.
Standards and certificates in the medical industry
The certificates that medical device manufacturers hold confirm compliance with advanced requirements.
The most important standard in the medical industry is ISO 13485 concerning the Quality Management System for Medical Devices, developed in line with ISO 9001, but further specifying its requirements. The standards can be used together or separately.
ISO 13485 has been developed for medical equipment manufacturers. Suppliers certified to this standard adhere to principles including quality management in the design, manufacture and assembly of medical devices, as well as risk management and inspection of manufacturing processes.
Printor has been working successfully with companies in the medical equipment manufacturing segment for many years. However, to meet the increasing demands, Printor decided to implement ISO 13485. The implementation procedure started this year and the company will undergo an audit process early next year to officially become certified to the medical standard.
PCB assembly in contract electronics manufacture for medical manufacturers
Medical equipment manufacturing companies should pay particular attention not only to certifications, but also to the comprehensive nature of an electronics supplier. Why? Because a broad service range – including PCB manufacture, component assembly using the THT or SMT methods, component handling: picking and storing, as well as testing of finished boards – reduces costs and streamlines the collaboration process.
Because PCB assembly for the medical industry must be reliable, the extent of testing is particularly important. PCBs can undergo electrical testing, automated optical inspection (AOI), ICT testing, functional testing and ionic purity testing. These are carried out to guarantee the highest quality.
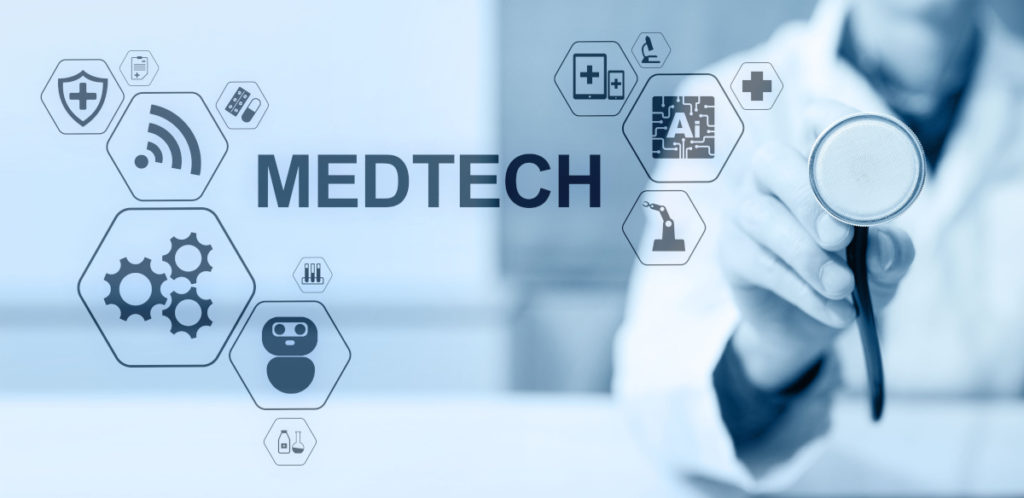
Criteria for selecting an electronics supplier for the medical industry
What matters most when choosing an electronics supplier? First and foremost, the service range – the broader it is, the greater the chance that the supplier will meet any necessary requirements, e.g. they will also handle the assembly of components in the target equipment, i.e. the final assembly of PCBs.
Equally important is the quality issue we have already mentioned. When choosing a supplier, you want to be sure that the supplier has the right machinery at their disposal, employs specialists and controls the manufacturing process at every stage. At the same time, they should ideally have prior experience working with companies in the medical sector, as this sector requires a unique approach.
Another crucial aspect is the quality of communication and customer service – responding promptly to enquiries and reacting to potential problems, advisory services, flexibility, and transparency. The supplier is supposed to be a partner who understands the client’s business and can act effectively.
If you are a medical equipment manufacturer looking for partners in contract electronics manufacturing, do not hesitate to contact us.
- final assembly of electronics as part of comprehensive electronics manufacture – https://printor.pl/en/offer/final-assembly-electronics/
- comprehensive electronics manufacturing service range – pcb manufacture, smt assembly, tht assembly, tests and additional services – https://printor.pl/en/offer/comprehensive-offer/